The following section describes each road system present in our project area. Even though our field reconnaissance time did not allow us to set grade lines in every road system we designed, descriptions for this roads were also made and can be found in the following sections.
10.5.1 Closer System
The Closer Mainline road system consists of one major road with several spurs, which access landings within the Closer and Schwing Ding timber sales. This road is located in the northwestern part of the planning area covering approximately 341 acres and spanning for 117 stations (2.2 miles).
The Closer Road spurs off the #10 road in the SW ¼ of the SW ¼ of Section 33 of T15N R06E. The road continues in a northwesterly direction until reaching the outer boundaries of the Closer timber sale. The road consists of three switchbacks. The first one is situated at the point from which it starts off from the #10 road and the other two are both located in saddles between ridges.
There are two major stream crossings which determine the location of this road. It was determined that the original stream crossing location at the first stream was too low, which later placed the road in wet, unstable slopes leading up to the second stream crossing. To avoid these potential problems, the initial stream crossing was placed upslope past the confluence of the stream creating yet another crossing. However, this placed the road on stable slopes for this portion of the road.
The RoadEng design files can be found on the data CD
\final_dnr_data\mark\Closer Mainline RoadEng Design
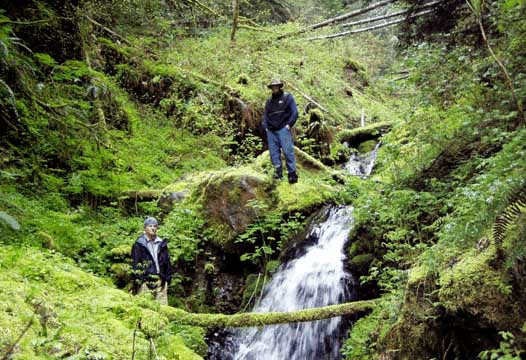
Figure 19: Mark and Colin stand near a fish blockage on the first stream crossed by the closer road. This blockage was approximately 400 feet up stream from the proposed road crossing.
It was determined that since the first stream crossing has deeply incised channels, that a bridge would the best solution in crossing. In addition, the DNR also has a portable bridge not currently being used. A detailed stream survey was done at this site in which a 3-D image of the stream was generated and then traversed.
From the second stream crossing on (station 40+22), the road runs pretty smoothly, not crossing any potentially unstable areas. It runs down this ridge on the other side of the second stream crossing until it reaches a saddle on which we have our second switchback. From this switchback, 58+16, the road stretches out in a northeastern direction until it hits one of our landings at station 67+30. From this landing location, on which there are remnants of old truck or railroad grades, the road continues along the landscape in a northern direction and then curves around the northeastern ridge of the Closer sale to come back into the flat, saddle area near which our second switchback occurred. From this switchback (station 100+98) the road climbs up the northwestern ridge of the closer sale until it reaches a landing on the northern facing slope of the eastern half of the closer sale (station 116+86, GPS verified).
As mentioned earlier, there are several spur roads contained within the closer system. Although these were never verified in the field they consist of relatively short distances and should be pretty inexpensive to construct when the sale is ready for harvest. The first spur runs about 5+13 stations northwest from the main road. The spur begins about 14+50 stations from the first stream crossing. The next spur road starts of in between our second stream crossing and our second switch back, about 8 stations north from the stream crossings and runs east for about eight stations. We find two more spur roads taking off from our landing location at station 67+30, one running north for about 5 stations and the other running west for about six stations in order to access another landing. Two more spurs take off in a western direction for about four and a half stations each starting at station 82+55. The last and final set of spurs stretch out south for about nine stations starting out at about seven and a half stations from our last switch back. Figure 20 shows the entire Closer road system shown in blue.
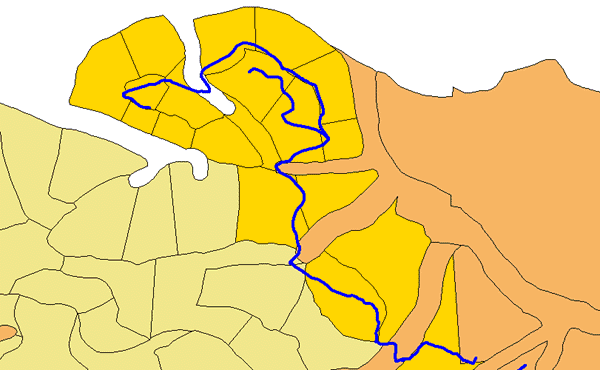
Figure 20: Closer road system in blue. The settings in orange will be using the Closer road system.
10.5.2 Mineral System
The Mineral Mainline System consists of two major stretches of road and a system of spurs. There are two major purposes for this road system. The first is to access the southwest part of the North Tahoma block, and the second is to connect the 24 Road with the existing Mineral Road system (Figure 21). This road system accesses over 900 acres of harvestable timber with approximately 550 stations of new construction.
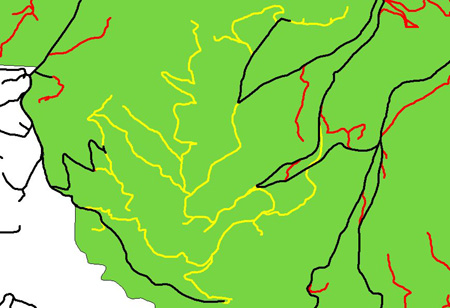
Figure 21: The yellow roads represent the Mineral road system.
The topography and slope stability of this area controlled the location of most of the proposed construction. There are several wet and unstable areas which we tried to avoid. We tried to stay away from these areas, because there are high maintenance fees of having roads in that area. Much of the road goes through steep side-slopes, which will make for high road construction costs due to the large volume of excavation.
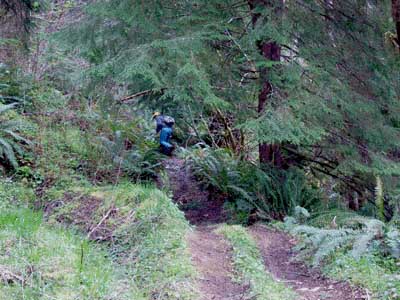
Figure 22: The lower existing Mineral road. After field verification it was determined that this road should no longer be used.
Two different routes were looked at to connect the 24 Road with the existing Mineral Road system (Figure 23). This was done so that were could compare and contrast two different options and chose the best one. Both of these roads took advantage of old railroad grades (Figure 24). Some maintenance will have to be done on these grades to stabilize the slopes.
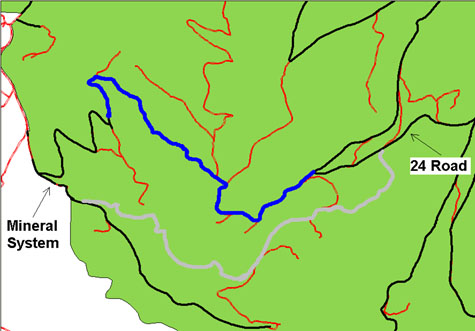
Figure 23: Upper (Blue) and Lower (Grey) Options for Proposed Mineral Mainline.
The first option that we looked at started approximately half a mile up the 24 Road and extended west to connect with the existing railroad grade in the Mineral system. There were multiple unstable areas (Figure 22) and difficult crossings (Figure 25) along this route.
Evidence of mass wasting and washouts were found along the length of the lower existing railroad grade (as seen on Figure 24), making its extensive use uneconomical. Several wet areas with alder trees and other water loving plants and were also found along the proposed route, indicating potential for future failure.
There were also two difficult stream crossings on this route with steeply incised channels (one is shown in Figure 25). These crossings would not require bridges, but the alignment must be pushed into the hill to reduce the fill height over the stream. This will result in large cuts.
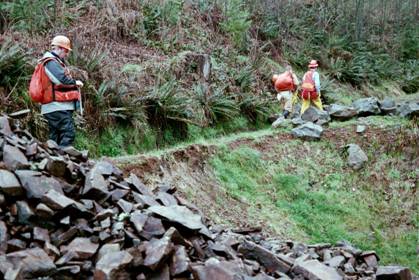
Figure 24: Failure on Old Railroad Grade.
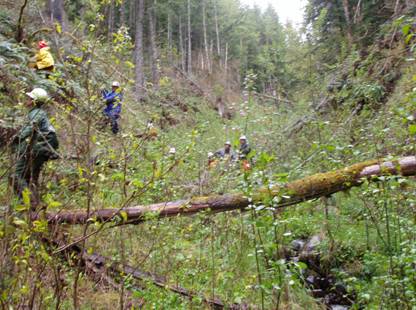
Figure 25: Difficult Stream Crossing.
The second option that we looked at started at the first switchback of the 24 Road and extended west, above the first option, to connect with the cork screw road of the Mineral system (Figure 23). The idea was to locate the route above the streams and wet areas that were in the lower part of the ridge.
There are a few engineering challenges in building this road. There were still several wet areas, with lots of alder that had to be crossed (Figure 26). Some of these locations were able to be avoided by moving the road up above the start of the wet area.
For 8+50 stations the road follows an existing railroad grade. There are two spots along this grade which have begun to become unstable due to a lack of water control (Figure 27). These two spots are characterized by deep stream channels. With careful road placement and appropriate culvert placement, these points can be crossed.
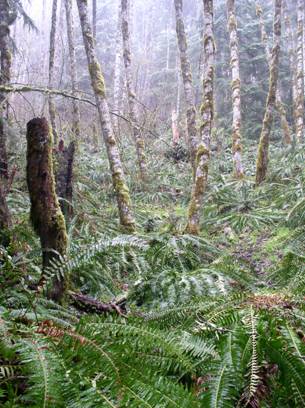
Figure 26: Potentially Unstable Area.
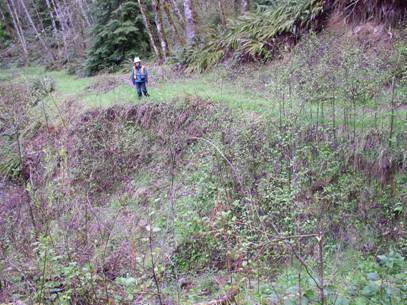
Figure 27: Failure of Old Railroad Grade.
In conclusion, both of the proposed routes connecting the Mineral system with the 24 road are difficult to construct and would require extensive maintenance following construction. Network analysis is needed to determine if savings in haul cost from routing trucks through the Mineral system (bypassing Ashford) will offset the significant road construction costs in this area.
10.5.3 West Mineral System
The West Mineral Road System consists of a one bypass as well as a few designed access roads (about one mile in length) combined with a system of spurs (Figure 28, in yellow). The major purpose for this road system is to access over 1,700 acres of harvestable timber with approximately 630 stations of new construction. The bypass route allows for two options for exiting the area, via the east wing or west wing.
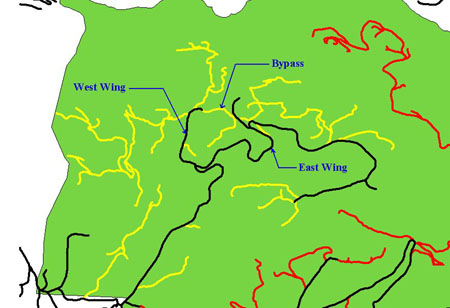
Figure 28: West Mineral Road System (Yellow).
The long designed access roads are necessary due to the limited extent of existing roads in this system (only 350 stations). Grade line was set in the field for the majority of these access routes. Limited grade line was set for spurs.
The bypass allows for trucks to exit on the west wing or the east wing of the existing portion of the West Mineral Road System. This will allow for Network calculations to find the haul route of least cost and sedimentation calculations to find the route of least sediment delivery.
No significant slope failures or hazardous areas for road construction were found in the West Mineral Road System. Due to the large extent of coverage in field work, no extensive slope failures are anticipated in other portions of the system. Existing railroad grades were used frequently due to good stability.
10.5.4 Ridge System
The ridge road system consists of one major road (the ridge road itself) and various spurs. This system access's the southern to southeastern areas of the North Tahoma block and it allows access into upwards of 1,893 acres and 82 settings. There are 469 stations of existing roads and 748 stations of planned roads within this system. With all roads combined totaling approximately 23 miles of roads within the system (Figure 29).
While the road primarily accesses the northern slope of the ridge it is located on the southern side due to the steep slopes and visual issues, caused by the close proximity to highway 706. There are two main spurs branching off the ridge road, one accessing more of the North Slope, and the other accessing the southwestern slopes of the ridge.
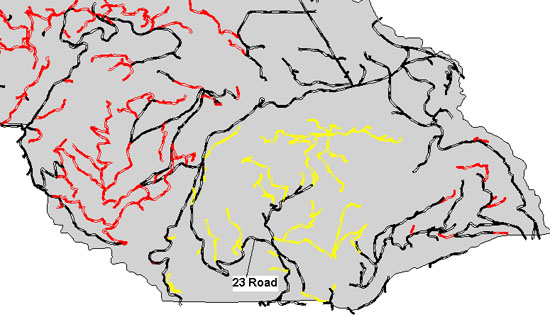
Figure 29: Location of the Ridge system leaving the 23 Road. The yellow roads are the ridge system.
The Ridge Road splits from the 23 Road in the NE ¼ of the SE ¼ of Section 9 of T14N R06E. The road continues in a northerly direction, and then curves to the west, from a saddle and continues along the ridge. The road ends when it reaches the nose of the ridge where the western most landing on the ridge is planned. The southwestern spur was originally planned to come off the existing spur just after it left the 23 road, but due to some stability issue it was broke into two separate spurs to access the necessary landings. The spur that accesses the rest of the North Slope leaves the ridge road at approximately station 37+00 and bears due west. The haul routes out of the ridge system and its spurs will, for the most part, be an adverse haul due to the high elevation of the spur coming off of the 23 road. Since there was no other way to access this area the adverse haul could not be avoided.
The Ridge road mainline never crosses any streams or wet areas thus stability is not an issue for the mainline. However the spur that accesses the southern to southeastern part of the region has some stability issues. Most of these stability issues were avoided by breaking the single spur into two different segments avoiding the unstable area. The other main spur was not field verified due to time constraints. There are various other short spurs leaving the ridge road that were not field verified. These are mainly short spurs that should be fairly inexpensive to construct.
The Ridge system is the largest road system within the North Tahoma planning area and accesses the largest acreage of all of the systems. Due to time constraints we were only able to field verify the mainline and one of the main spurs. So there is some extensive field work to be done in this area. Do to visual impacts and the steepness of the terrain some of the spurs in this area may have to be moved and or some adjustments made during the field verification.
10.5.5 Reese Creek System
The Reese Creek Road System consists of one major cutoff road and a system of spurs. There are two major purposes for this road system (Figure 30). The first is to provide a cutoff for the 24 road, eliminating 2 stream crossings and approximately 62 stations of parallel roads. The second purpose of this road system is to access 570 acres of harvestable timber with approximately 134 stations of new construction.
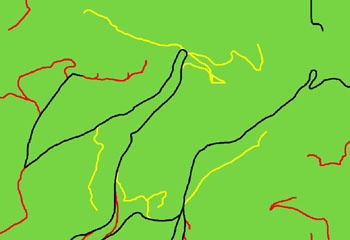
Figure 30: Reese Road System (Yellow).
With so few new stations, the Reese Creek is a small road system. However, the cutoff would help reduce haul time down the 24 road. Most of the area is harvested with a mobile tower and can be accessed with existing roads. The few planned spurs help reach landings for primarily central tower settings as well as a few ground based and mobile tower settings.
Only a minority of the grades in this area were ran in the field since there was only one proposed change to the main haul route. The 24 cutoff was set with no major difficulties. A minor area of concern is the initial routing off the 24 road, which is adjacent to a stream buffer. The area here is steep and construction will be difficult next to the wet areas of the buffer.
The next grade line set in the field was an alternate route accessing the southern landing of the Schwing B sale. This spur runs to the south of the proposed route, increasing the spread between the spurs for this area in about the same length of construction.
No significant slope failures or hazardous areas for road construction were found in this area. However, as mentioned, field work was limited in the Reese Creek Road System, so problem areas may exist.
10.5.6 Catt Creek System
The Catt Mainline road system is the smallest road system of our road network. It consists mainly of several small spurs that extend off of the existing road network. These roads are located in the southeastern part of the planning area, covering approximately 439 acres (Figure 31).
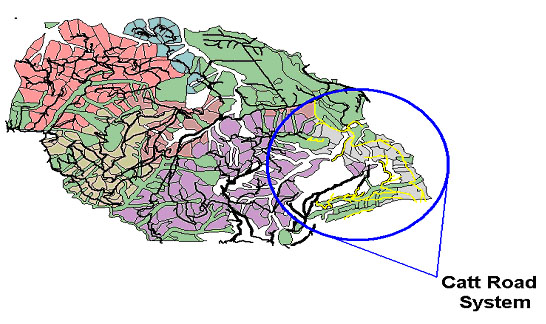
Figure 31: Catt Road System.
The Catt system consists of 587 stations of roads (Figure 32). There
are 108 stations of new roads that we have planed for that area. Due to
the time constraints of the quarter, the only road in this system that
had field verified was the last 15 stations of the "Ridge road." There
were no stream crossings on any of the new roads that were laid out.
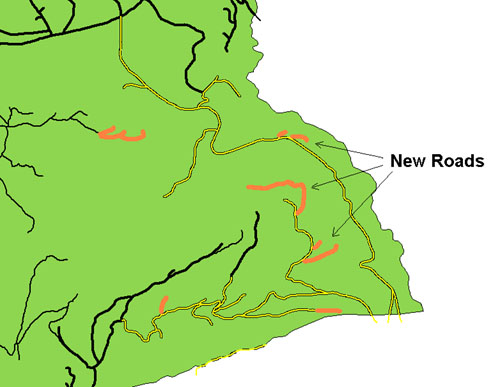
Figure 32: New Roads on Catt System.
|